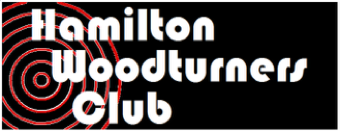
~ A dedicated club promoting the art and craft of Woodturning ~
Best Practice
Lathe Alignment
Before starting any spindle work, it is important that the headstock and tailstock are properly aligned. This is best achieved by loosening the headstock locking lever, inserting an alignment tool into the headstock, then sliding the tailstock up so that it fits onto the alignment tool. When lathe alignment has been achieved then re-tighten the headstock locking lever.
Alternately, fit a drive spur to the headstock and a live centre to the tailstock, then slide the tailstock up towards the headstock so the points can be used to achieve alignment.
This procedure also needs to be done before using a Jacob's Chuck (e.g. to drill into/through the workpiece), in order to ensure that the drilled hole remains true to the centre of the workpiece.
Tool Sharpening
The secret to a good, clean wood cut is to have really sharp tools, so sharpening your chisels is key. It is recommended that you sharpen your chisels at the beginning of every woodturning session, and as needed during the session.
We are grateful for the following sharpening advice given by Terry Scott (Timberly) and Woodcut Tools in the following videos:
Note that different woodturners (even professional ones) have their own preferences when it comes to choosing their "go-to" chisel, and the angles that they use when sharpening the different types of chisel. This doesn't mean that some of them are wrong in their choice; it is largely a matter of personal preference - what works for them. However, when sharpening the chisels provided in the Club's workshop, members MUST adopt the settings and advice given by our Tutor and that have been endorsed by the Club's Committee. Failure to follow these instructions will result in our tools ending up with multiple bevels on each chisel. It will also mean that the chisels will need to be sharpened more often, removing more metal in order to get a consistent surface on the bevel, which will reduce the life of the tool. You are free to sharpen the chisels in your own workshop at home to whatever specification you prefer, but when using the Club's chisels you MUST adopt the Club's rules.
Lathe Speed
Safety is the watchword here. Running a lathe at too high a speed for the workpiece is a potential hazard for the turner and any others in the workshop. The workpiece could come off the lathe, or shatter - each piece becoming a missile that can do serious harm. Even if the outcome does not cause injury, the workpiece is likely to end up beyond repair.
The main factors that need to be taken into consideration when selecting the lathe speed include the following:
- the characteristics of the workpiece to be turned (its dimensions and weight)
- whether the workpiece is of a regular shape (i.e. is it balanced when attached to and slowly rotated on the lathe)
- whether the workpiece has any cracks, defects, or loose bark that could break off
- the method of attaching the workpiece to the lathe (faceplate, chuck, steb centres)
- the tools/accessories to be used (type of chisel, jacob's chuck for boring into the workpiece; power sanding)
Centripetal force is always present when a workpiece turns on a lathe. This force is greater the higher the speed of the lathe; and the greater the diameter of the workpiece. So as a basic rule, the greater the diameter of the workpiece, the slower the speed setting needs to be on the lathe. If the workpiece is of an irregular shape, then start off with a slow speed setting. Where possible improve the workpiece before mounting it on the lathe (e.g. cut a round blank using a bandsaw; cut off unwanted irregularities; remove loose bark; glue cracks).
There can be a temptation to turn at a higher speed setting, as this can result in a cleaner cut (e.g. with a skew chisel). However, it is important to remember to set the speed to suit the size of the workpiece.
Other reasons to moderate the lathe speed include: the initial cuts on a rough workpiece - this can be a strain on the turner, the lathe and the workpiece; vases, goblets or bowls with a thin wall, the thinner the wall the weaker the workpiece becomes
Some chucks have a maximum speed constraint due to the way the workpiece is attached, namely a Longworth Chuck, and Cole Jaws. These should not be used above 600rpm. A Jacob's chuck should be used with a lower speed of 200-400rpm to prevent the drill and workpiece from overheating
Remember to always wear the appropriate safety gear when turning, including a good quality faceshield.